Creating a Talent Production Line
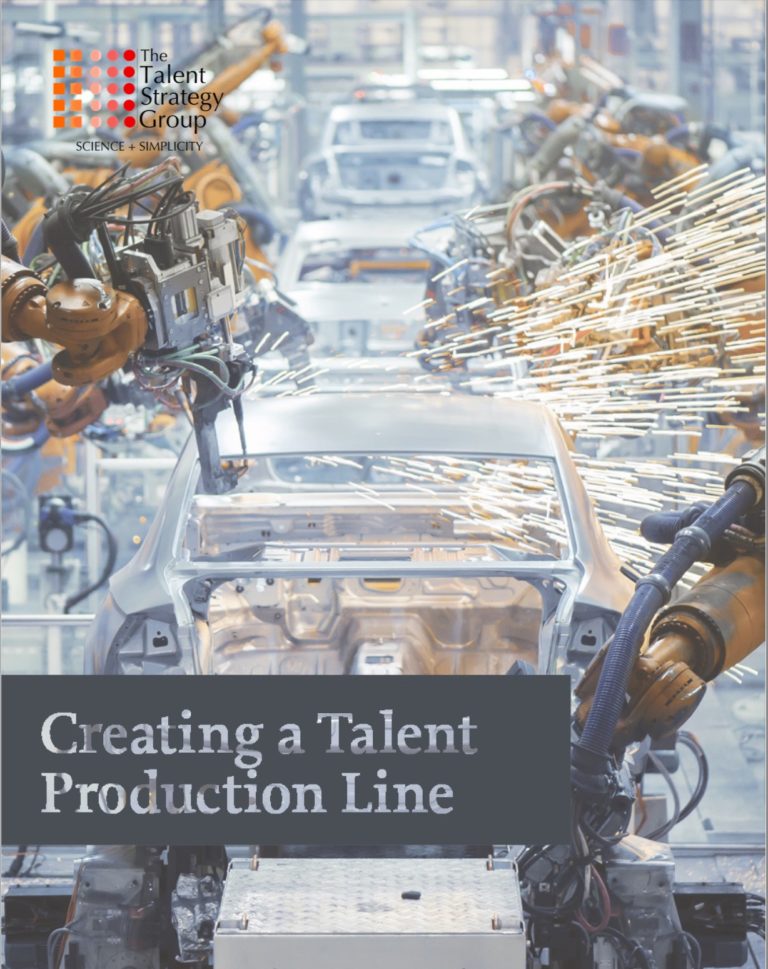
Acme Motors CEO sat down at the conference table across from VP of Production Brad Smith. Brad was responsible to design and operate the production line for Acme’s proposed XL1000 sedan. The XL’s success was critical to the company’s future profitability and the CEO had questions about how it would be produced.
“Brad,” the CEO began, “Tell me how you’ll determine the manufacturing specs for the XL1000.”
Brad smiled confidently. “I’ve recently bench-marked three other car companies,” he said proudly. “The specifications they use to build their cars seem reasonable, so we’ll use the same ones to build the XL1000.”
The CEO look quizzically at Brad but continued with his questions. “Do we have enough of the right raw material to produce the XL1000?”
“We have plenty of aluminum in the warehouse,” Brad replied, “and I’m sure some of it is suitable to make the XL1000.”
The now agitated CEO loudly tapped his pencil on the conference table. “But the XL1000 will have a fundamentally different shape and performance requirements than our other cars. Are you confident that this same aluminum will work?”
“I can’t predict that,” Brad responded, “but this aluminum has performed well for us in the past, so I assume we can build an XL1000 from it too.”
Rapidly losing confidence in Brad’s abilities, the CEO probed for more details. “Tell me how you plan to actually produce the XL.” Brad sensed that this was the time for him to ask for an investment.
“Well,” he started, “there is this really cool new aluminum stamping machine. I haven’t seen it work yet, but everyone on LinkedIn says that it’s great! It’s just $5 million dollars and it might be helpful.”
The now angry CEO leaned forward. “But not all of the aluminum needs to be stamped,” he snapped, “and it certainly takes more than that to produce a car!”
“We absolutely must have XL1000s coming off the production line within 5 years or this company will fail! We need a disciplined, repeatable process for manufacturing this car. Can you promise me that we’ll have high quality XL1000s in 5 years?”
Brad hesitated. “My manufacturing team can provide a lot of resources and tools that support building a car. They’re all highly engaged. I’m not sure what else we can do.”
It’s difficult to imagine that conversation actually taking place in any manufacturing environment. After all, we would expect someone who’s responsible to manufacture a product to clearly understand what they’re building, the raw materials it requires and how to create a consistent, disciplined process to manufacture it.
So, if your CEO asked you to describe how HR plans to manufacture your company’s next generation of leaders, would your response be any better than Brad’s?
The Need for A Talent Production Approach
In too many organizations the plans for producing talent are as shaky as Brad’s plan for producing the XL 1000.
These organizations haven’t clearly defined the type of talent they need.
They can’t accurately predict which current talent can be shaped into what’s needed for the future. They don’t understand the sequence of actions that will produce the desired capabilities.
We can do better. We can manufacture talent with the same care and dedication that we use to manufacture any other valuable product. We can create talent production lines that use disciplined and consistent production processes to build leaders to our organization’s exacting specifications.
Most importantly, we can promise our organizations that they will have the capabilities they need, on time and on budget.
But, this also does not mean, of course, that we should treat people like widgets. If fact, our call is for companies to put at least the same care, discipline and investment into producing people as they do into their products and services!
But, this also does not mean that the talent production line is a cute analogy for leadership development. It is a real, disciplined, repeatable manufacturing process to produce high quality talent.
Creating the Talent Production Line
An effective HR team should be able to design and operate an actual talent production line. By “actual”, we mean that just as an automobile production line produces cars, a talent production line must produce talent.
Creating your talent production line requires four steps:
1. Set Your Specifications
When you run a talent production line you’re manufacturing a highly customized product. Your first step is to clarify your customer’s needs and to create specifications for a product that can actually be built.
The more design specifications you have for a product the more difficult, expensive and time consuming it is to manufacture. The key question to ask is, “What are the 4 or 5 truly differentiating capabilities our talent needs in order for our organization to win in the future?”
What does great look like? To define “great” throw away your competency cards and ask your customers to describe what they want the finished product to do. You’ll hear their specifications described in real-world language that makes it easier to design an actual production process.
Your description of “great” is the heart of your production process. It should guide how you assess your raw material, how you design your production line and how you measure success.
We believe that a traditional competency model is not effective for this process. We advise our clients to use a Success Model to identify the vital few capabilities, and avoid confusing “good citizen” behaviors with those that truly differentiate high performance.
2. Assess your Raw Material
Success in this production step requires understanding what talent is in your organization and if it’s suitable for producing your product.
The two key questions to answer are:
- Do you understand what raw material is available? What capabilities, behaviors and skills currently exist in your organization? A regular and fact-based talent review process should provide the needed information. It’s a manager’s responsibility to make accurate talent predictions in this conversation.
- How much of this raw material can be built into your specifications? A more challenging step is to assess whether this raw material has the potential to become your desired product. What facts do you have that suggest that it can be transformed into the new specifications? Are you predicting based on personality traits? Demonstrated behaviors? Emerging capabilities? The accuracy of your prediction is critical. A higher level of accuracy today means that your talent investments are more likely to generate a return.
We provide guidance for conducting high quality talent reviews in our article “Six Steps to Great Talent Reviews.”
3. Build your Production Process
We are fortunate in HR to have research that tells us which tools most effectively build employees’ skills and capabilities. Our challenge is that we don’t always apply the right tool at the right time – either through lack of planning or lack of courage.
We know that the 70/20/10 balance for developing employees (70% of growth comes from experiences, 20% from exposure/feedback and 10% from formal classroom learning) is backed by good science.
Does that 70/20/10 represent the balance of how you develop talent in your organization?
To ensure you can produce the talent you’ve specified, you must be able to answer:
- Do you have a process that can manufacture this talent? If you have the right specifications and raw materials, do you know what series of feedback, assignments, coursework, coaching, et al. is guaranteed to manufacture it successfully?
- Do you have the right “machinery”? If you are clear about the manufacturing process, do you have the tools available to manufacture the product? For example, if a key production step involves moving a leader through a specific role, will that role always be available when needed?
- Is the machinery arranged in a way that produces talent? A key aspect of a production line is that there is a logical flow of materials. Raw material enters the process at the front of the production line and product emerges at the other end. Does your talent manufacturing process consistently move talent through a well-defined series of production activities?
- How will you keep this production line moving? Congratulations if you’ve built a talent production line that’s capable of producing the leadership or management product you need. How do you plan to keep that production line moving? If it takes three assignments, two projects and one educational experience to produce talent to your specifications, you need to ensure that the talent moves through those manufacturing steps at the right pace. Who’s accountable for the production line actually producing talent?
4. Ensure Effective Distribution
Getting your finished talent to the right role or location can be more difficult than it might appear. The manager of that talent might not want to release it. The talent might decide that it won’t or can’t go. Another department might step in front of the intended customer and take the product.
To make sure that your finished product gets to the correct role or location, you need to answer:
- Do you know how to get the product to where it’s needed? Do you have the ability to quickly and easily move this product around the globe or to a new role at a low cost? We find a key enabler of this is that your executive team collectively manages top talent.
- How will you control distribution? If you build a great product, it will be in high demand. What process will you have to logically allocate the product? If your product isn’t in high demand, this is a good time to reexamine your specifications.
Enabling the Production Line
If you can affirmatively answer these production questions, then your company is poised to produce higher quality talent more quickly than your competitors.
But, just because you’ve built a talent production line doesn’t mean that it’s actually going to run.
Two other elements must be in place:
- Increase Talent Production Capabilities: HR and talent leaders in your company must be skilled talent production managers. They must stop thinking of themselves as craftspeople who carefully assemble individual leaders by hand.
Your line leaders must understand the production process and their role in producing talent. Their capabilities as talent builders – what we would define as the Talent6 – must be elevated to a high level.
Those capabilities are described in our two classic articles, “Building Great Talent Managers: The 4+2 Model” and “Becoming a Talent6 Leader.” We also teach these capabilities at our Talent Management Institute.
- Take Accountability: As with any other manufacturing process, while many hands are involved, someone is ultimately responsible for building a complete, high quality product. If HR builds and operates the talent production line, it’s only fair that they take a large share of the responsibility for its successful operation.
Line leaders must also be held accountable for increasing the quality and depth of talent in their teams. We believe that this is second most important priority for your people mangers after delivering high performance.
This means that HR’s metrics should be production outcomes (i.e. number of GMs delivered on-time at quality standards), not process measures (ran a development course eight times). Leaders’ metrics must be the continual improvement of capabilities and succession depth.
Our article, “The Accountability Ladder” provides a process and suggestions for how to set accountability at the right level.
When you apply a manufacturing mindset to producing talent, it also allows you to apply other helpful manufacturing tools. Lean Manufacturing states that using resources for any goal that doesn’t create value for the end customer is wasteful and should be eliminated.
If you audited your talent management and leadership development activities against that standard, how many of them could prove their value?
Doing Better
We can help our companies produce more better talent faster by applying a disciplined manufacturing approach to development. We know how to set specs, assess talent, produce talent and distribute talent. All we need now is the, discipline, willpower and capabilities to make it happen.